O que quer saber?
Perguntas e respostas
ENERGY-EFFICIENT TECHNOLOGY
We are here to support you, not restrict you. We know that creative freedom is important in architecture, so you don't have to work with us exclusively. However, we guarantee that you will love IZODOM technology and want to design only in it.
Absolutely not. We focus on partner relations and want to be a business support for you, not a limitation. However, we guarantee that you will want to build only in passive technology as soon as you learn its benefits and the simplicity of implementing subsequent projects.
Absolutely not! Each element is perfectly matched to another and after filling with concrete, it gains full durability. Thanks to this, you can be sure that the house will retain its quality for years and the structure will remain solid regardless of the passage of time.
The use of IZOEnergy or IZOPassive technology generates savings on heating or cooling the building in the range of 50 to 80% in comparison to traditional technologies. Thanks to the excellent insulation parameters, the lack of thermal bridges, the warmth stays in the house and does not escape outside. To compare and get to know the approximate heating costs, just use our calculator.
The great advantage of the IZODOM technology over traditional technologies is the construction time. An open shell house will be built in 5 weeks. While a brick building will take even 2-3 years to be built. Another advantage of IZODOM is the possibility of construction in virtually all weather conditions. Construction can also be carried out in winter.
The most interesting references of IZODOM are:
3.000 energy-efficient villas in 2009 in the United Arab Emirates.
the palace of the King of Morocco with an area of 10.000 m2,
500 social homes near Lille in northern France (government project),
passive house estate in Scotland,
estate of 247 apartments near Warsaw [Latchorzew estate] 1998,
passive house in central Siberia Omsk, Surgut, Kazakhstan,
construction beyond the Arctic Circle, e.g. in Tromso in northern Norway,
houses with a demand of 4kWh/m2/year in France 2012, a block of 5 floors 12kWh/m2/year in Lithuania 2015 and many other energy-saving residential buildings,
construction of a medical clinic in the passive standard in Lubliniec,
the largest complex for the production of mushrooms, several dozen buildings with a length of 150 m and a wall height of 8 m (in Poland and Ukraine, in the years 1995 - 2015)
IZODOM boasts over 20,000 reference buildings around the world.
The tallest building in IZODOM technology is an 11-storey block of flats built in 1996 in Moscow. It required the use of high-strength concrete and additional reinforcement on the lower floors, and a 20 cm wide core for the first few floors.
Concrete radiation is a myth.
Some people ask us about radiation in concrete buildings - but this is not supported by facts.
Most of the radiation measured in buildings comes from natural sources. This is radiation occurring in the environment, e.g. it results from the presence of radon in the ground.
The average level of radiation in such a building will not be higher than the level of radiation in a building made of ceramic bricks, so our health will not be at risk.
The main source of radiation is household appliances, not concrete elements.
Buildings built in traditional technology do not require special ventilation. When building a traditional house, in which brick walls are replaced with hollow ICF block walls, traditional gravitational ventilation is enough.
Through leaks or special openings in the windows, fresh air enters the room, it is heated above the radiator, takes moisture, odors and carbon dioxide and escapes through the ventilation grilles. In residential buildings, where the air exchange rate is equal to 4, the entire volume of air in the room is exchanged 4 times per hour, causing large losses of thermal energy. This phenomenon occurs regardless of what the house is made of.
In order to save heating energy, in energy-efficient and passive houses, devices are installed to recover heat from the air, maintaining the same guaranteed circulation. Mechanical ventilation, recuperators are responsible for providing fresh air and minimizing energy losses, and they are not directly related to the type of walls. What's more, it reduces the amount of allergens in the air.
In turn, the PN-EN 12831 standard also defines the minimum multiplicity of exchanges in the building at the level of 0,5 exchanges per hour / depending on the number of people, it is 0,6-1,0.
Wall breathing - the mythical transport of moisture through the wall.
In the 1990s, the myth of "wall breathing" emerged in some markets. It comes down to the expectation that the wall is supposed to transport moisture from the house to the outside.
There were statements that mineral wool and bricks drain moisture well, while polystyrene is tight and does not drain it - hence, moisture and fungus will probably appear on the walls.
This is a myth that has not been confirmed by research or observations of buildings.
There is a lot of moisture in buildings - a family of 4 produces 11 kg of water per day in the form of steam (by cooking, bathing, breathing)! That's as much as 330 kg per month.
This amount of moisture must be discharged outside by ventilation - traditional or mechanical.
Walls - regardless of whether they are made of brick, concrete and polystyrene, have no effect on the amount of moisture in the building.
The only unit of building physics close to "breathing" is the kinematic water vapor diffusion coefficient, which describes the rate of steam penetration through a given material. The fact is that polystyrene is very poorly permeable to water vapor. However, a "breathable" wall - brick and mineral wool, 30-40 cm thick, with external plaster and painted from the inside with paint, has such a low total diffusion coefficient that transporting 11 kg of water through the wall would take 3 months. Fungi grow where water vapor condenses. This happens where it meets a cool place - in places where there are thermal bridges. Most often, these are connections of ceilings with walls, connections of external and internal walls, lintel beams.
To have a guarantee of a healthy and dry apartment, it is enough to have efficient ventilation and use construction technology without thermal bridges - such as IZODOM.
The wall is supposed to be primarily a barrier to heat and moisture. The fact is that if we start washing and cooking at the same time, the ventilation will not keep up with the removal of moisture, but - contrary to popular belief - it is not the walls that start to drain water to the outside, but the phenomenon of buffering occurs. Plaster, furniture, floor, curtains, people's clothes absorb moisture, and when the extraordinary source of moisture ceases to supply it, these buffer elements "dry" and this amount of moisture is carried out through the ventilation.
The term thermos is often confused with the tightness of the building.
Energy-efficient and passive houses require compliance with standards regarding the tightness of the building. It is easy to check it by carrying out the so-called "Blower Door Test".
Proper air flow in such a house is guaranteed by mechanical ventilation, which, combined with heat recovery, provides savings of 50% on the costs of heating and cooling the building.
See how much your home will save.
In some countries, a myth has arisen that the building must be not be tight, that the tightness of a building causes moisture, and the so-called "thermos effect". Although hardly anyone is able to specify what it means exactly.
The airtightness of a building is very important. Having a traditional ventilation system that requires fresh air, we must have special ventilation gaps in the windows to allow fresh air inside. Sealing the vents in the windows or covering the exhaust ventilation grilles will stop the air circulation in the house.
The airtightness of a building is related to the ventilation system, and micro-gaps or air vents in the windows, not the walls.
Energy-efficient and passive buildings have very small heat sources and must be airtight.
We often encounter the question of whether polystyrene oxidizes or disappears? This is a myth that exists in some markets.
Styrofoam does not oxidize, does not disappear, does not dematerialize. It can melt or dissolve, so it is important to avoid organic solvents (benzene, toluene, xylan, etc.), high temperatures above 90ºC directly affecting new blocks. New foam plastics must be protected from direct UV rays.
The myth comes from manufacturing errors, when in the 70's polystyrene was glued with adhesives (they contain organic solvents). During repair works in the 1990s, burnt holes were observed on the surface of boards coated with glue, interpreting this as the phenomenon of "oxidation".
Accumulation of heat means storing energy in the walls - obtained, for example, from heating the interior of the building with a fireplace. However, this is an inefficient method of heating, which is why accumulation in the walls is now abandoned in favor of heating the air enclosed in the volume of the building. Accumulation stoves, which accumulate heat, e.g. by heating up when we have a lower electricity tariff, and give it back during the remaining period, are popular.
Heat storage in walls is not efficient for several reasons:
losses due to the penetration of heat from the air into the wall and giving it back to the air,
heat escape to the inside of the building structure by transferring it to other structural elements,
very high energy demand for heating several dozen tons of construction materials.
The IZODOM technology is designed for modern, intelligent control systems that turn on the air heating before the household members return and lower the temperature after they leave.
Styrofoam is pure plastic, has no nutritional value - it is not food for organisms. Neither for bacteria, nor fungi and mold, and the admixtures of anti-fire substances used in BASF raw materials make these materials not liked by rodents.
A layer of plaster and a reinforcing mesh, which are also used in traditional construction on polystyrene under the external finishing, additionally protect against rodents. Due to the fact that since the beginning of the company's existence, we have not recorded a single information about any problem with rodents, for years we have not recommended the use of a double mesh reinforcing and protecting plasters in the strip 30-40 cm above the ground level.
We offer stationary training at the company's headquarters or via the Zoom platform, depending on the participants' preferences.
We offer training for:
Individual Customers
Business Clients
Architects and Constructors
All current dates are available at the link.
The trainings concern the IZODOM technology, construction principles, construction issues, insulation and energy efficiency of buildings.
An example training agenda is as follows:
What is the IZODOM technology?
Why is it worth to build in the IZODOM technology?
Changes in construction law
Reference buildings
Overview of the elements of the IZODOM technology
How to build? What to heat with? What cladding?
Myths about IZODOM technology
Benefits of using the IZODOM technology
We conduct training in several languages. If you have a specific demanding project or a problem, it is worth informing us about it in advance, then we will prepare a training on the given topic.
Of course. We are happy to answer any questions, doubts we always help. Designers receive from us, in addition to the possibility of free training, a set of information materials - 12 information notebooks that explore all the technical guidelines. We also offer telephone, or email assistance from our designer.
We also invite you to free training courses for architects. A schedule of current dates is available at the link.
IZODOM technology is simple, does not require the use of specialized equipment, so it very often happens that buildings are implemented by inexperienced companies. However, in order to make the construction last as short as possible - and the cost of labor was minimal we recommend using experienced companies that have already implemented construction in our technology.
Therefore, we recommend using recommended and authorized contractors.
Due to its LEGO-like construction, our customers often opt for economy construction.
To avoid mistakes during construction, we encourage you to attend a training course on IZODOM technology.
It takes IZODOM a maximum of 10 working days to prepare an offer for the purchase of elements for fittings.
The IZODOM company is in the top three of the most serious producers in the European market. Having significant competitors in France and Germany, IZODOM is distinguished by the richest offer of elements. As the only company, it produces a complete system from the foundation to the roof. As the first company in the EU, it certified products at the German Institute for Building Technology DiBT, obtaining the CE mark. IZODOM cares very much about the quality of the manufactured elements, especially resistance to cracking, fire resistance, shape stability, testing them in its own laboratory and in 3 external laboratories, which is confirmed by the ISO mark issued by TUV, since 1994.
In Poland, Izodom 2000 Poland is a monopolist when it comes to ICF technology. It is the only company in Europe that produces a set of polystyrene fittings for building houses (foundation slab, exterior walls in three different variants depending on the energy class you want to achieve, load-bearing interior walls, partition walls, floor slab and roof cap insulation). In Poland, apart from ICF, our main competitors are companies producing "bricks", blocks and other traditional building materials.
IZODOM products are manufactured exclusively from the raw materials of the largest chemical concern BASF, which guarantees the high quality of the manufactured components. IZODOM also supports designers with 12 information booklets and guidelines for designers and constructors. In this respect, it is a leader in this part of Europe.
Savings on heating and cooling the building. This advantage means that investors no longer have to be afraid of rising prices and can safely look into the future by paying minimal energy bills. Regardless of the heating source used, the energy demand will be so small that the costs of heating or cooling the building, including heating the hot utility water, will be at a level as much as 80% lower than in the case of traditional technology.
Completeness of technology - materials for foundations, walls, ceilings of the whole house can be provided by one manufacturer. Quick preparation of the offer along with transport to the construction site takes several days.
Speed of construction - Combining lightweight, easy-to-handle blocks and filling them with ready-mix concrete makes this a fast, all-weather building system. In the case of a simple project, laying the formwork and filling with concrete of one storey can be done even in one day. The building in the open shell is ready in 4 weeks.
IZODOM walls do not require additional insulation - which shortens the construction time and reduces costs.
No thermal bridges and high insulation parameters. Foundation slab U=0,14 W/m2K, walls U=0,15 or 0,10 W/m2K, roof insulation U=0,15 up to 0,11 W/m2K.
Ease of construction - you do not need a specialist team or heavy equipment to build the house. All you need is training or instruction at the construction site, which is offered by the technology manufacturer. Patented block locks allow for quick erection of walls, without the use of mortars, adhesives or metal clamps. The construction is so simple that a large part of investors, not working in the construction industry on a daily basis, decide to build on their own, using the economic method, assembling blocks with family and friends.
High quality of elements - this is due to 30 years of experience in the production of materials for the construction of energy-efficient houses and high-quality raw material. Styrofoam used for the production of IZODOM elements is supplied by the inventor of polystyrene, a company that first introduced the popular EPS to the market, and then invented NEOPOR. Additionally, the density of the raw material used for the production of blocks is the highest on the market. For comparison, a typical facade polystyrene has about 3 times lower density. This is confirmed by numerous certificates held by the company.
Ecology - research was conducted comparing the life cycle of the product, in accordance with ISO 14040, in terms of the erection phase of a single-family building in the IZODOM technology and a compatible building built of hollow bricks and mineral wool technology. The comparative indicator was the total emission of greenhouse gases marked with the CO2 symbol. The results of the research indicate a reduction of CO2 emissions by 51.3% in favor of the IZODOM technology. The company also takes a number of actions related to the used product to protect the environment. The calculated set of elements necessary to complete a project is delivered to the construction site. This eliminates the need to cut wall blocks and to produce waste. Projects using the IZODOM technology use a smaller number of formwork and supports or eliminate them completely. Only steam and electricity are used during production. No chemicals are used. All waste is recycled, no industrial wastewater is generated during production. In addition, thanks to the very high insulation parameters of the IZODOM system, houses designed in it are energy-saving and passive. The energy used to heat or cool the house is optimized accordingly.
IZODOM wall elements are produced in two variants: white EPS and gray Neopor. Both are supplied by BASF.
Neopor, thanks to the addition of graphite, has better insulation parameters than white EPS by about 15% - with the same thickness of the insulation layer. The mechanical strength is the same.
The difference is the lower insulation of EPS elements. Gray elements insulate better.
The elements of the foundation slab are made of Peripor (BASF) and dyed yellow. This does not change its insulation parameters. Peripor is an expanded polystyrene with improved parameters of resistance to moisture and very high resistance to compression.
Produkty IZODOM od 2007 posiadają certyfikaty oraz dopuszczenie ETA 07/117 czyli Europejskie Dopuszczenie Techniczne wydane przez Niemiecki Instytut Budowlany DIBT.
Dokument można zweryfikować szukając na stronie Europejskiej Organizacji ds. Dopuszczeń Technicznych www.eota.eu
Proces produkcji podlega nadzorowi w ramach Zakładowej Kontroli Jakości, Polskiego Instytutu Techniki Budowlanej, i co roku jest audytowany.
Mając ważny dokument ETA oraz pozytywną opinię wydajemy znak CE dla naszych produktów ściennych. Elementy fundamentowe i dachowe podlegają pod normę EN 13172 i EN 13163, stąd na podstawie aktualnych badań wydajemy Deklarację Zgodności.
ETA i znak CE pozwala nam na sprzedaż elementów na terenie całej Europy.
Over 30 years ago, the IZODOM system offered 6 blocks with a thickness of 25 cm. Currently, it offers over 200 of them in 5 thicknesses. The company has several patents. It offers components for all building elements - from foundations to the roof. The elements are manufactured in an increased concrete pressure class.
30 years of experience and observation of over 20.000 construction sites have allowed us to constantly improve our products.
Manufactured for 30 years, the MC 2/25 element has been improved more than 8 times.
In Poland, energy-efficent and passive construction is unfortunately still a niche. Of the 120.000 building permits (data from 2021), only about 5,000 (about 4%) are for energy-efficient and passive buildings. However, over the course of about 10 years, there has been a very big change in people's openness to the IZODOM technology. This is due to greater consumer awareness, greater emphasis on environmental protection, the desire to build quickly without the use of heavy equipment, huge savings on heating costs compared to traditional technology - which in the era of constant increases in energy prices is becoming the number one topic. Abroad, especially in western markets, our technology has been present since the 1990s. We have 20 partners in 20 foreign markets. The western market has been developing energy-saving construction for a long time. We have numerous references from around the world, e.g. in social housing, where, thanks to the choice of our technology, savings in heating are huge. At the beginning of the company's activity, sales were at the level of 90% export, 10% Polish market. Now it is 50 to 50%. We are extremely pleased that the Polish market has matured for wise, responsible construction, which will not only make life easier for future investors, but will also contribute to the protection of the environment and natural resources. The European Union introduces new amendments regarding the technical conditions for the requirements for new buildings. With the entry of the WT 2021 standard, each new building must meet a number of requirements. Taking into account all these factors and the constant, drastic increases in energy prices, lack of workforce, pressures of fast construction, we believe that passive and energy-saving construction and IZODOM technology are the only good choice. Such construction will not be a fashion or a trend, but a necessity.
Yes, we are certified by the Passive House Institute in Darmstadt. Our products meet the stringent requirements for building materials by various institutes and standards: Darmstadt, MinEnergie, EneriePlus, LEED, BREEM in terms of insulation and load capacity. The values are confirmed by tests that are recorded in the European Technical Approval ETA from DIBT Berlin. In addition, we are the Ambassador of the Polish Institute of Passive Houses and Renewable Energy.
The expected life of the building is a minimum of 150 years. The life of the structure corresponds to the life of the concrete core. Studies of the "weathering" of the wall carried out by the BASF concern simulating 120 years, and observations of boreholes from 60-year old walls erected in the technology of lost formwork indicate higher resistance of IZODOM walls to weathering, heating, freezing, moisture, radiation - than concrete unprotected from weathering, such as concrete in the structures of bridges, viaducts. The core is protected on two sides from significant jumps in temperature, humidity, as well as the effects of rain and UV rays. In IZODOM wall, the concrete core works in such comfortable conditions that are impossible to achieve in any other construction technologies. Winter - summer: the temperature of the core changes by only a few degrees Celsius. In any other wall, the temperature difference can be as much as several tens of degrees
The durability of polystyrene foam insulation is estimated at several hundred years. The insulation is virtually indestructible. The material is protected by a layer of plaster against UV rays, and resistance to freeze/thaw cycles, moisture, not subject to biological corrosion makes the hollow block wall practically indestructible. From mechanical impacts, the IZODOM wall is protected from the inside with, for example, gypsum plaster, and from the outside with clinker, or, for example, plaster and reinforcing mesh.
The acoustics of the Izodom walls meet the standards for residential construction, the Ra1 and Ra2 coefficients are given in the appendix. Walls requiring high acoustic resistance, e.g. in hotels, require additional sound insulation. You can, for example, install a wooden grate on the wall, put mineral wool between the beams and cover it with a double plasterboard.
External finishing | Internal finishing | Rw (C1, C2) | RA1 | RA2 | |
MC 25 | Thin layer mineral finishing | Gipsum cardboard 12,5mm | 43(-2,-4) | 41 | 39 |
MC 25 | Thin layer mineral finishing | Gipsum cardboard 12,5mm | 43(-2,-4) | 41 | 39 |
MC 25 | Thin layer mineral finishing | Gipsum cardboard 12,5mm | 43(-2,-4) | 41 | 39 |
MC 35 | Thin layer mineral finishing | Gipsum cardboard 12,5mm | 43(-2,-4) | 41 | 39 |
MC 45 | Thin layer mineral finishing | Gipsum cardboard 12,5mm | 43(-2,-4) | 41 | 39 |
MCF MCFU 25 | Thin layer mineral finishing | Gipsum cardboard 12,5mm | 43(-2,-4) | 41 | 39 |
MCF MCFU 25 | Thin layer mineral finishing | Gipsum cardboard 12,5mm | 43(-2,-4) | 41 | 39 |
Izodom will provide you with a free quote for the elements. This involves calculating the type and quantity of blocks, and at the same time estimating the volume of concrete and the cost of transportation to the construction site. For floor/ceiling elements, in addition to the blocks, we also offer the main rib reinforcement - with the length specified in the project.
The rest of the labor and material costs - reinforcement, roof structure, assembly - are offered by a local construction company.
The offer is made for the desired wall insulation thickness. Interior walls, floor slab or foundation walls, ceilings, roof insulation, interior partitions - are quoted separately for each structural element of the project to enable the customer to make an informed purchase decision on the Izodom products he is interested in.
Foundation slab - an individual design drawing is prepared for each customer, the polystyrene elements of the slab are cut to the required dimensions in our factory according to the drawing, the elements are numbered and entered into the drawing. The elements for the construction of the slab are cut as our product and delivered to the construction site ready for installation.Izodom will provide you with a free quote for the elements. This involves calculating the type and quantity of blocks, and at the same time estimating the volume of concrete and the cost of transportation to the construction site. For floor/ceiling elements, in addition to the blocks, we also offer the main rib reinforcement - with the length specified in the project.The rest of the labor and material costs - reinforcement, roof structure, assembly - are offered by a local construction company.The offer is made for the desired wall insulation thickness. Interior walls, floor slab or foundation walls, ceilings, roof insulation, interior partitions - are quoted separately for each structural element of the project to enable the customer to make an informed purchase decision on the Izodom products he is interested in.Foundation slab - an individual design drawing is prepared for each customer, the polystyrene elements of the slab are cut to the required dimensions in our factory according to the drawing, the elements are numbered and entered into the drawing. The elements for the construction of the slab are cut as our product and delivered to the construction site ready for installation.
Expanded polystyrene has been known since 1955 when BASF introduced it to the market. Cement has been known since Roman times, since the 19th century concrete has been used as the basic construction material. The formwork, the forms that give concrete shape, are just as old. The formwork made of wooden boards built on site, prefabricated system formwork, aluminum system formwork boards, etc. are commonly used.
The idea of building with Izodm is based on building monolithic concrete or reinforced concrete walls, in formwork that is not dismantled and remains as part of the wall. Izodom formwork elements have two functions: first they are forms for concrete, and then they insulate the constructed wall. The elements are not dismantled, which is why the technology is sometimes called insulating permanent formwork. The first houses built in the technology of insulating, permanent formwork were built in Germany and Sweden in the 1950s, when polystyrene boards were used to build the formwork [instead of wood] filled with concrete. In fact, the idea of permanent formwork construction is as old as concrete.
COSTS AND SAVINGS
The cost per m2 of construction using IZODOM technology may vary depending on the thickness of the element in question and local market conditions, i.e. the price of steel, concrete or the construction crew.
In order to provide the most reliable information on the cost of purchasing our materials, we offer a free quote.
Podstawą do przygotowania przez nas dokładnej oferty są
dimensioned plans of all storeys including the dimensions of window and door joinery
rzut konstrukcji stropów,
wszystkie przekroje,
elevation views
These data can be sent to us as files: pdf., jpg., or dwg.
If you have not yet purchased a design, you can ask the design office to provide you with these drawings for a quotation.
If you do not yet have a design of your choice, we encourage you to use the option on our website.
Dom powinien być przede wszystkim energooszczędny i trwały, a prawdziwy „koszt domu” należy liczyć wraz z wydatkami na ogrzewanie przez kolejne lata. Technologia tradycyjna to gorsze jakościowo materiały, które zmuszają nas do znacznych, corocznych wydatków na ogrzewanie.
W związku z dużą podwyżką tradycyjnych materiałów budowlanych cena 1m2 domu wykonanego w technologii IZODOM nie różni się znacząco od kosztu m2 w technologii tradycyjnej.
Należy również spojrzeć na całościowy koszt budowy. Porównując dodatkowo:
- szybkość budowy- w technologii IZODOM budowa domu to kilka tygodni- koszt robocizny będzie znacząco niższy.
- brak konieczności docieplania ścian- wiąże się to z oszczędnością czasu oraz dodatkowych kosztów robocizny.
- cena robocizn taka sama dla każdej klasy energetycznej (grubości ścian). Jeśli chcemy wybudować dom energooszczędny bądź pasywny, zmieniamy tylko kształtki, a cały dalszy proces budowy nie ulega zmianie.
- ogromną oszczędność kosztów, jeżeli chodzi o ogrzanie oraz chłodzenie budynku podczas całego okresy jego eksploatacji.
- brak mostków termicznych - ciepło nie ucieka z domu.
Biorąc pod uwagę wszystkie te czynniki, możemy stwierdzić, że budowa domu energooszczędnego lub pasywnego w technologii IZODOM będzie o wiele bardziej ekonomiczna, niż wykorzystanie tradycyjnych metod.
Koszt domu to konglomerat kosztu materiałów budowlanych i instalacyjnych, transportu i robocizny itp. Ważny jest też standard, na jaki Inwestor się decyduje – czy dom ma być przede wszystkim tani, czy energooszczędny i trwały, co wiąże się z doborem materiałów o normalnej lub lepszej jakości. Kolejną rzeczą są ceny robocizny zależne od sytuacji na lokalnym rynku budowlanym.
My, jako producent materiałów IZODOM możemy określić koszt dla elementów płyty fundamentowej, ściennych, stropu oraz objętości betonu konieczne do zalania płyty fundamentowej, ścian i stropów, ale potrzebujemy do tego konkretnego projektu.
„Dom o powierzchni 120m2” może mieć bardzo prostą konstrukcję, albo odznaczać się dość skomplikowanym układem pomieszczeń, co będzie istotnie rzutowało na cenę materiałów. Dlatego też pracujemy na konkretnym projekcie domu, i unikamy stwierdzeń, że materiały na dom 120m2 będą kosztowały X, albo Y.
Oferujemy darmową wycenę zakupu naszych elementów. Wystarczy zgłosić się do nas z wybranym projektem
IZODOM pomaga określić koszty elementów szalunkowych dla poszczególnych części budynku: płyty fundamentowej, lub ścian fundamentowych; ścian wewnętrznych i zewnętrznych, stropów, dachu – na podstawie przedstawionego projektu. Oferujemy również transport: dostawę na plac budowy w dowolne miejsce na świecie. Prace budowlane i dodatkowe materiały wymagają skosztorysowania przez lokalną firmę budowlaną. Cennik poszczególnych elementów systemu jest dostępny dla Klientów. Firma bezpłatnie przygotowuje kompletne zestawienia elementów szalunkowych na podstawie przesłanych nam projektów. Zestawienie dotyczy ilości elementów, ich cechy oraz objętość, potrzebną do planowanego transportu na plac budowy oraz ceny transportu. Obliczenia te wykonujemy bezpłatnie.
.
CONSTRUCTION
We, as a manufacturer of materials in IZODOM technology, deal exclusively with the supply of elements, but we work with contractors and architects, we have a network of associates throughout the country - so we will help you find the best one.
IZODOM technology is adapted to a variety of projects, even multi-apartment blocks, offices or businesses! You have more than 100 elements at your disposal, which with a good design from an architect can create virtually anything. The concrete structure is suitable for both houses and larger buildings!
Nothing is wrong - you can still contact our consultant and ask your questions. Building a house is not an "overnight" decision, so if you want to learn more about IZODOM technology first, we are here for you!
The ceiling can be laid 28 days after the walls have neen filled with concrete. This is the time when the concrete in the walls reaches the designed load-bearing capacity. In practice, it is possible after 10-14 days, depending on the temperature and humidity.
Experienced contractors place the formwork under the ceiling on the second day and pour concrete on it, because until the ceiling formwork is removed, it is the formwork, not the wall, that supports the weight of the ceiling. With this solution, the walls and ceiling bind at the same time.
When the investor decides on prefabricated ceilings - such ceilings can also be laid after a few days, because the 15 cm of concrete core, which has not yet been 100% dry, already has sufficient load-bearing capacity to support the weight of the ceiling.
Changing the construction technology is possible.
In single-family housing, in most countries, changing the construction technology does not require a change in the building permit, only an appropriate annotation from the constructor performing the adaptation of the ready project to local conditions is required.
In case of any doubts regarding the adaptability of the project, the constructor should be consulted.
In our system there is no problem to install a fireplace.
Because polystyrene can withstand temperatures up to 70 degrees - chimneys, saunas, fireplaces, are necessary to be additionally isolated from the blocks, e.g. with the use of 5 cm of mineral wool with aluminum foil glued, or another way selected by the designer.
As a facade finish, the same solutions as when insulating buildings with polystyrene boards, i.e. thin-layer plasters - mineral, acrylic, silicone, silicate, are most often used. Our Customers also use brick lining, clinker tiles or facades made of stone slabs. With heavy finishes, such as stone facades, various types of panels, they should be anchored in accordance with the manufacturer's recommendations - on Fischer expansion bolts, concrete core expansion bolts, or properly supported on a foundation.
We do not use lime plasters on facades, because they have different thermal expansion than polystyrene and can degrade after some time. The photos of our reference houses show wooden facades, clinker cladding, system facades - there are no limits.
There are no contraindications to make basements of houses in the IZODOM technology. What's more, we recommend our elements for making basement walls.
Why?
Because the basement walls must withstand not only the weight of the building applied from the "top", but also the ground pressure from the "side" - durable concrete or reinforced concrete walls, which are the core of the IZODOM wall - will easily withstand such loads. An additional advantage is stopping the cold penetrating from the ground, which is blocked by a thick insulation layer. Waterproofing can be applied directly to the element.
We quite often encounter the construction of basements in our technology for buildings in frame construction.
We also recommend our IZOCeiling ceilings for the implementation of horizontal partitions between the basement and the ground floor - in order to keep the heat in the residential part, unless we want to heat the basement or garage.
IZODOM products made of white raw material - EPS without external plaster finish, left uncovered, exposed to UV rays, degrade on the surface at a depth of 1-1.5 mm. Styrene polymer - polystyrene breaks down into a monomer. The white wall becomes covered with a yellow coating, which, in turn, constitutes a natural barrier against further interference of UV rays.
After two years, an unplastered wall will be covered with dust - styrene monomer, and in an unplastered state it will look the same after 2 and after 10 years.
Before plastering, as with any other surface, it will have to be cleaned and the dust will have to be removed.
IZODOM materials are resistant to changes in temperature and air humidity.
Warunki atmosferyczne nie wpływają negatywnie na materiał systemu IZODOM. Elementy należy przykryć nieprzezroczystą folia chroniąc je przed zanieczyszczeniem i zabezpieczyć przed działaniem wiatru przyciskając je np. stalowymi podporami, paletami. Wilgoć, deszcz, śnieg nie pogarszają właściwości produktów.
Betonowanie ścian orientacyjnie trwa około pół dnia.
Wypełnienie betonem ścian domu o powierzchni 150m2 zajmuje do 4-5 h. Beton układa się okółkowo, warstwami po 75-100cm wysokości ściany. Przed betonowaniem zaleca się usztywnienie szalunku podporami, mającymi na celu utrzymanie pionu ścian w czasie betonowania.
Dom 150m2 to około 150 m2 ścian.
1m2 ściany wypełnia się 125L betonu/m2. Oznacza to, że 1m3 wystarcza na 8m2 ściany.
Czyli 150m2 ścian to 18,75 m3 mieszanki.
Betonuje się z prędkością podawania betonu 9-11m3/h [bardzo wolno]. Czyli 150m2 zabetonujemy w czasie 2h.
In accordance with the guidelines prepared by the Lodz University of Technology - in most cases it was recommended: C20/25 concrete, with a grain size of 16 mm and a densely plastic consistency with a minimum amount of water and the addition of a plasticizer.
Currently, it is C20/25 concrete, with a maximum grain size of 8mm and a consistency of S3-S4, according to EN 206-1: 2003. Or - according to EN 12350-3:2001 VeBe time between 11 and 30 seconds. To improve plasticity, it is still recommended to use plasticizers for concrete. Concrete must not be diluted with water.
The use of a grain size of up to 8mm avoids the formation of cavities in the concrete.
Concrete strength should be between C16/20 and C50/60 according to EN 206-1. If the European standard EN 206-1 is not applicable, it is acceptable to use concrete in accordance with the national regulations in force at the place of use, but with a compressive strength within the above range.
The requirements for the consistency of the concrete mix must be strictly observed - it is not allowed
use liquid mixtures, because the pressure and buoyancy of such concrete leads to deformation of the polystyrene wall skeleton.
It is allowed to use concrete mixes of V1 or V2 consistency, according to PN-EN 206+A2: 2021-08 Concrete. Part 1: Requirements, properties, manufacturing and compliance. It is comparable to a dense plastic or plastic consistency according to the previous definitions. Consistency measurement, made in accordance with PN-EN 12350-3:2001 Concrete mix testing. Part 3: Testing
consistency by the VeBe reflow method, should show a reflow time of 11 to 30 seconds. - according to the guidebook no. 2.
The most common damage is breakage of interlocks (IZOClick) or breaking of a fragment of a long block. Damage to the interlocks causing the formation of gaps - should be filled with mounting foam.
Damaged fragments of elements are cut off with a wood saw, recovering an undamaged fragment.
Changes in the project, such as bricking up the window, or vice versa, adding a window, are allowed even during construction.
It is possible to make changes in the IZODOM system. Building the formwork, before filling with concrete, we can verify the location of windows and doors. If we want to modify something, it is enough to brick up the openings with Izodom blocks, or dismantle a fragment of the formwork to create a new opening. All you need is a wood saw.
After concreting, the openings can be bricked up, but it's important to pay attention to maintaining the thickness of the insulation layers. Creating new holes requires cutting and treatment of the new hole.
Styrofoam is pure plastic, has no nutritional value - it is not food for organisms. Neither for bacteria, nor fungi and mold, and the admixtures of anti-fire substances used in BASF raw materials make these materials not liked by rodents.
A layer of plaster and a reinforcing mesh, which are also used in traditional construction on polystyrene under the external finishing, additionally protect against rodents. Due to the fact that since the beginning of the company's existence, we have not recorded a single information about any problem with rodents, for years we have not recommended the use of a double mesh reinforcing and protecting plasters in the strip 30-40 cm above the ground level.
IZODOM technology is a very universal technology. You can easily combine IZODOM elements with other building materials. You can design any solutions for internal load-bearing and partition walls and join them with IZODOM external walls. IZODOM walls combine well with any floor/ceiling technologies - Filigran, prefabricated, wooden, monolithic concrete slabs, etc.
The foundation slab can be used as a foundation for any technological solutions used by designers, including prefabricated, brick or wooden houses.
Combining technologies - in particular connecting Izodom walls and ceramic walls - requires the use of steel stirrups coming from the concrete core and placing them between the layers of bricks. Lightweight partition walls, i.e. aluminum profiles with cardboard gypsum board, only require anchoring of expansion bolts in the concrete core in the Izodom wall. The solution recommended by us is the construction of all types of walls, i.e. external, internal, load-bearing and partition walls in the Izodom system and concreting them simultaneously.
Only such a construction will ensure adequate monolithicity and rigidity of the structure. In such case all kinds of connections (wall bends, connections of external and internal walls, corners) will be made in the most durable way.
When laying subsequent layers of hollow blocks, window and door openings should be modeled - with the use of plugs closing the formwork.
In passive and energy-efficient buildings [U=0,15W/m2K, or 0,10W/m2K, i.e. 20 or 30 cm of insulation), the continuity of insulation cannot be violated. In the IZODOM technology, windows and doors should be installed in the external layer of insulation.
In standard buildings [U=0,23, i.e. 15 cm of insulation], in window and door openings, the frames are installed using wooden wedges and expansion bolts anchored in concrete, and the joints are sealed with foam.
We fasten windows and doors using the so-called warm installation. We use polystyrene dowels here (e.g. Fischer dowels for mounting in polystyrene). Since the loads carried by polystyrene plugs are lower than those of concrete screw plugs, the number of polystyrene plugs must be greater. After screwing the dowels into the polystyrene, we fix the windows and doors to them.
It is necessary to follow the recommendations of the window manufacturer.
When a concrete pump, in the case of a traditional 15 cm thick core, the diameter of the concrete pumping pipe should be reduced to 100 or 80 mm. The pipe should be inserted as deep as possible to minimize the free fall height of the concrete.
Concreting is carried out in a circular pattern - i.e. in layers with a maximum height of 80 - 100 cm. We know from practice that it takes 1-1,5 hours to lay the first layer of concrete. During this time, the laid mix begins to "harden" slightly, so that loading it with the weight of the next layer of concrete has a lesser effect on increasing the hydrostatic pressure on the side walls of the permanent formwork.
Concreting of the wall core from a great height should be avoided for two reasons.
Firstly, the concrete falling from a height of 3 meters delaminates, thus losing the assumed strength.
Secondly - concrete falling from a great height causes high dynamic forces that can deform the geometry of the concrete wall and in extreme situations - can cause cracking of the side wall of the polystyrene formwork.
The elements are designed to create and fill formwork with a height of one storey - up to 3 meters. This means that 12 layers of blocks can be placed before concreting.
Concrete is fed with a pump, a container attached to a crane, or from a silo.
The elements are manufactured in such a way as to withstand the pressure of concrete placed up to the height of one storey. The locks connecting the blocks, lacings and the production method itself guarantee strength and tightness.
The elements do not require mortar, glue or any internal fasteners recommended by other permanent formwork manufacturers.
IZODOM's offer includes supports with a height of 2.7 m and higher supports up to 5 m in height, facilitating work and guaranteeing the verticality of the walls. The supports are designed in such a way that it is possible to adjust the supports, and thus plumb the constructed wall, thanks to the so-called turnbuckle.
The width of the concrete core - a structural element - regardless of the thickness of the insulation layer is 15 cm. This is enough thickness to erect buildings up to 22m high. Walls in single-family houses are usually made of C20/25 class concrete, using a minimum amount of reinforcement.
We reinforce, as in traditional technologies - lintels and the tie beam. Additional reinforcement is: strengthening the corners of the external walls by placing vertically two rods with a diameter of 10mm in them, the places where internal and external walls are joined and knee walls. The walls do not need to be connected with the foundation with reinforcement, we do not place the reinforcement in the wall itself - a concrete wall is more durable than brick walls.
Wall reinforcement appears in buildings with a height of more than 3 storeys, in knee and gable walls. It is worth paying attention to our technical drawings. In the case of complex, high or special-purpose buildings: e.g. cold stores, industrial buildings, schools - the need for reinforcement is decided by the constructor designer, who should use our information guidebooks, which we provide free of charge.
What does the reinforcement in the IZODOM technology look like?
The design of the building structure is made by a local designer with valid design qualifications. Calculations are made on the basis of current standards for concrete or reinforced concrete construction, e.g. Eurocode 2.
Lintel beams and tie beams are reinforced - in the same way as in traditional technologies. The corners are also reinforced - by placing two ø10mm rods vertically in them and placing stirrups made of 6mm wire along the axis of the walls. Wall reinforcement is used in three-, four-storeys and higher buildings.
The decision on the amount and type of reinforcement is always taken by the designer - the author of the project, or the person adapting the finished project. Information guidebooks prepared by Izodom and the Department of Concrete Construction of the Lodz University of Technology are helpful for this - they are available in Polish, English, German. We have published as many as 12 of them, and they facilitate static calculations for foundation slabs, swimming pools, walls in residential and industrial buildings, ceilings, roofs, etc. These guidebooks are available by e-mail in pdf files in Polish, English, German and Russian.
The system allows the construction of swimming pool walls, load-bearing and partition walls, walls of industrial buildings, as well as foundation slabs, ceilings and roofs.
The principles of construction with IZODOM technology are presented at the training course or on our website
We also encourage you to visit our channel on You Tube, where there are numerous instructional videos.
Of course. We are happy to answer any questions, doubts we always help. Designers receive from us, in addition to the possibility of free training, a set of information materials - 12 information notebooks that explore all the technical guidelines. We also offer telephone, or email assistance from our designer.
We also invite you to free training courses for architects. A schedule of current dates is available at the link.
IZODOM technology is simple, does not require the use of specialized equipment, so it very often happens that buildings are implemented by inexperienced companies. However, in order to make the construction last as short as possible - and the cost of labor was minimal we recommend using experienced companies that have already implemented construction in our technology.
Therefore, we recommend using recommended and authorized contractors.
Due to its LEGO-like construction, our customers often opt for economy construction.
To avoid mistakes during construction, we encourage you to attend a training course on IZODOM technology.
1m2 of IZODOM wall is filled with 125 L of concrete that is 1/8m3 of concrete.
In other words, 1 m3 of concrete is enough to build 8 m2 of wall.
W trakcie układania kolejnych warstw pustaków należy wymodelować otwory okienne i drzwiowe – z użyciem zatyczek zamykających szalunek.
W budynkach standardowych [U=0,23 to jest 15cm izolacji] w otworach okiennych i drzwiowych ramy mocujemy przy użyciu klinów drewnianych i kołków rozporowych kotwionych w betonie, połączenia uszczelniamy pianką.
W budynkach pasywnych i energooszczędnych [U=0,15W/m2K, lub 0,10W/m2K, to jest 20, lub 30cm izolacji), gdzie ciągłość izolacji nie może być naruszona montaż odbywa się w zewnętrznej warstwie izolacji.

Okna i drzwi mocujemy z zastosowaniem tzw. ciepłego montażu. Stosujemy tu kołki do styropianu (np. kołki do montażu w styropianie firmy Fischer). Ponieważ obciążenia przenoszone przez kołki do styropianu są mniejsze niż przez kołki wkręcane w beton, ilość kołków do styropianu musi być większa. Po wkręceniu kołków w styropian mocujemy do nich okna i drzwi. Koniecznie trzeba się stosować do zaleceń producenta okien.
Most popular films
Szkolenie Stacjonarne
Krótki opis, Spieniony polistyren znany jest od 1955 kiedy to BASF wprowadził go na rynek. Cement znany jest od czasów rzymskich, od XIX betony stosuje.
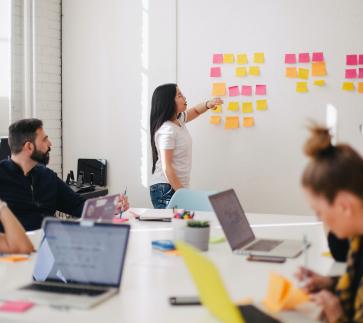
Szkolenie Stacjonarne
Krótki opis, Spieniony polistyren znany jest od 1955 kiedy to BASF wprowadził go na rynek. Cement znany jest od czasów rzymskich, od XIX betony stosuje.